Advantages Of GTAW: Unlocking The Potential Of Gas Tungsten Arc Welding
Gas Tungsten Arc Welding (GTAW), commonly known as TIG welding, has become one of the most versatile and precise welding techniques in the modern manufacturing industry. This process offers unparalleled advantages for a wide range of applications, from automotive to aerospace and beyond. If you're looking to understand the benefits of GTAW and how it can revolutionize your welding projects, this article will provide all the answers you need.
GTAW is not just a welding technique; it's an art form that combines precision, control, and quality. Its ability to produce clean, high-quality welds makes it a favorite among professionals in various industries. Understanding the advantages of GTAW can help you make informed decisions about its applications in your projects.
In this comprehensive guide, we'll explore the numerous benefits of GTAW, its applications, and why it stands out among other welding methods. Whether you're a beginner or an experienced welder, this article will provide valuable insights into the world of Gas Tungsten Arc Welding.
Read also:Angela Alvarez New S Exploring The Rise Of A Talented Artist
Table of Contents
- Introduction to GTAW
- Advantages of GTAW
- Applications of GTAW
- Comparison with Other Welding Methods
- Equipment Needed for GTAW
- Safety Considerations in GTAW
- Cost-Effectiveness of GTAW
- Environmental Impact of GTAW
- The Future of GTAW
- Conclusion
Introduction to GTAW
Gas Tungsten Arc Welding (GTAW), also referred to as TIG welding, is a welding process that uses a non-consumable tungsten electrode to produce the weld. The process involves creating an arc between the electrode and the workpiece, which melts the base metal and forms a strong, high-quality weld. GTAW is renowned for its precision and ability to produce clean, aesthetically pleasing welds.
Key Features of GTAW
One of the standout features of GTAW is its versatility. It can be used on a wide range of materials, including stainless steel, aluminum, magnesium, and copper alloys. Additionally, GTAW allows for precise control over the welding parameters, making it ideal for intricate and delicate welding tasks.
Another key feature of GTAW is its ability to produce welds without the need for filler material, which is particularly useful for thin materials where filler is not required. This results in cleaner and more aesthetically pleasing welds, making GTAW a preferred choice for projects where appearance is critical.
Advantages of GTAW
The advantages of GTAW are numerous and make it one of the most sought-after welding techniques in the industry. Below, we explore the top benefits of using GTAW in your welding projects.
Precision and Control
One of the primary advantages of GTAW is the level of precision and control it offers. Welders can adjust the current, arc length, and gas flow to achieve the desired weld quality. This level of control is particularly important in applications where accuracy and consistency are critical.
Clean and High-Quality Welds
GTAW produces clean, high-quality welds with minimal spatter and distortion. The use of inert gases such as argon or helium protects the weld area from contamination, ensuring a strong and durable bond. This makes GTAW ideal for applications where appearance and structural integrity are paramount.
Read also:Who Is Letitia James Partner A Comprehensive Look Into Her Life And Relationship
Versatility in Material Compatibility
GTAW is compatible with a wide range of materials, including metals that are difficult to weld using other methods. Its ability to handle non-ferrous metals like aluminum and magnesium makes it a versatile choice for various industries, from automotive to aerospace.
Applications of GTAW
GTAW finds applications in numerous industries due to its versatility and precision. Below are some of the key industries where GTAW is extensively used:
- Aerospace: GTAW is widely used in the aerospace industry for welding critical components such as airframes and engine parts.
- Automotive: In the automotive sector, GTAW is employed for welding exhaust systems, chassis components, and other critical parts.
- Marine: The marine industry relies on GTAW for welding ship structures and offshore platforms, where durability and corrosion resistance are essential.
Specific Applications
GTAW is also used in specific applications such as pipe welding, where its ability to produce clean and strong welds is crucial. Additionally, it is widely used in the fabrication of pressure vessels and heat exchangers, where leak-tight joints are required.
Comparison with Other Welding Methods
While GTAW offers numerous advantages, it's important to compare it with other welding methods to understand its strengths and limitations. Below, we compare GTAW with some of the most common welding techniques:
GMAW (MIG Welding)
GMAW, or MIG welding, is faster and more efficient than GTAW, making it suitable for high-volume production. However, GTAW provides better control and produces cleaner welds, making it preferable for precision work.
SMAW (Stick Welding)
SMAW, or stick welding, is more forgiving and easier to learn than GTAW. However, GTAW offers superior weld quality and is better suited for thin materials and delicate work.
Equipment Needed for GTAW
To perform GTAW effectively, you'll need the right equipment. Below is a list of essential tools and materials required for GTAW:
- Tungsten Electrode
- Inert Gas Supply (Argon or Helium)
- GTAW Welding Machine
- Welding Torch
- Protective Gear (Gloves, Mask, and Apron)
Tips for Choosing Equipment
When selecting equipment for GTAW, consider factors such as the type of material being welded, the thickness of the material, and the required welding parameters. Investing in high-quality equipment will ensure better results and longer durability.
Safety Considerations in GTAW
Safety is paramount when performing GTAW. Below are some safety tips to keep in mind:
- Always wear appropriate protective gear, including gloves, a welding mask, and a fire-resistant apron.
- Ensure proper ventilation to prevent the buildup of toxic fumes and gases.
- Regularly inspect equipment for wear and tear, and replace damaged components promptly.
Common Safety Hazards
Some common safety hazards associated with GTAW include exposure to ultraviolet radiation, electric shock, and inhalation of fumes. Proper training and adherence to safety protocols can minimize these risks.
Cost-Effectiveness of GTAW
While GTAW equipment can be expensive, the long-term benefits often outweigh the initial costs. The precision and quality of GTAW welds reduce the need for rework and repairs, resulting in cost savings over time. Additionally, GTAW's ability to handle a wide range of materials makes it a cost-effective solution for many industries.
Factors Affecting Cost
The cost of GTAW depends on several factors, including the type of equipment used, the skill level of the welder, and the complexity of the project. Investing in high-quality equipment and training can lead to better results and reduced costs in the long run.
Environmental Impact of GTAW
GTAW has a relatively low environmental impact compared to other welding methods. The use of inert gases reduces the risk of contamination and ensures cleaner welds. Additionally, GTAW produces minimal waste and emissions, making it an environmentally friendly choice.
Steps to Minimize Environmental Impact
To further reduce the environmental impact of GTAW, consider using renewable energy sources to power your equipment and recycling materials whenever possible. Proper disposal of welding fumes and gases is also essential to protect the environment.
The Future of GTAW
As technology continues to advance, the future of GTAW looks promising. Innovations in welding equipment and techniques are enhancing the efficiency and precision of GTAW, making it even more attractive to industries worldwide. The development of automated GTAW systems is also expected to increase productivity and reduce labor costs.
Emerging Trends
Emerging trends in GTAW include the use of robotics and artificial intelligence to improve welding accuracy and consistency. These advancements are expected to revolutionize the welding industry, making GTAW an even more valuable technique in the years to come.
Conclusion
In conclusion, the advantages of GTAW make it a superior choice for a wide range of welding applications. Its precision, versatility, and ability to produce high-quality welds set it apart from other welding methods. Whether you're working in the aerospace, automotive, or marine industry, GTAW offers numerous benefits that can enhance the quality and efficiency of your projects.
We encourage you to explore the world of GTAW further and consider its applications in your welding projects. Don't forget to share your thoughts and experiences in the comments section below. For more informative articles on welding and related topics, be sure to explore our website. Happy welding!
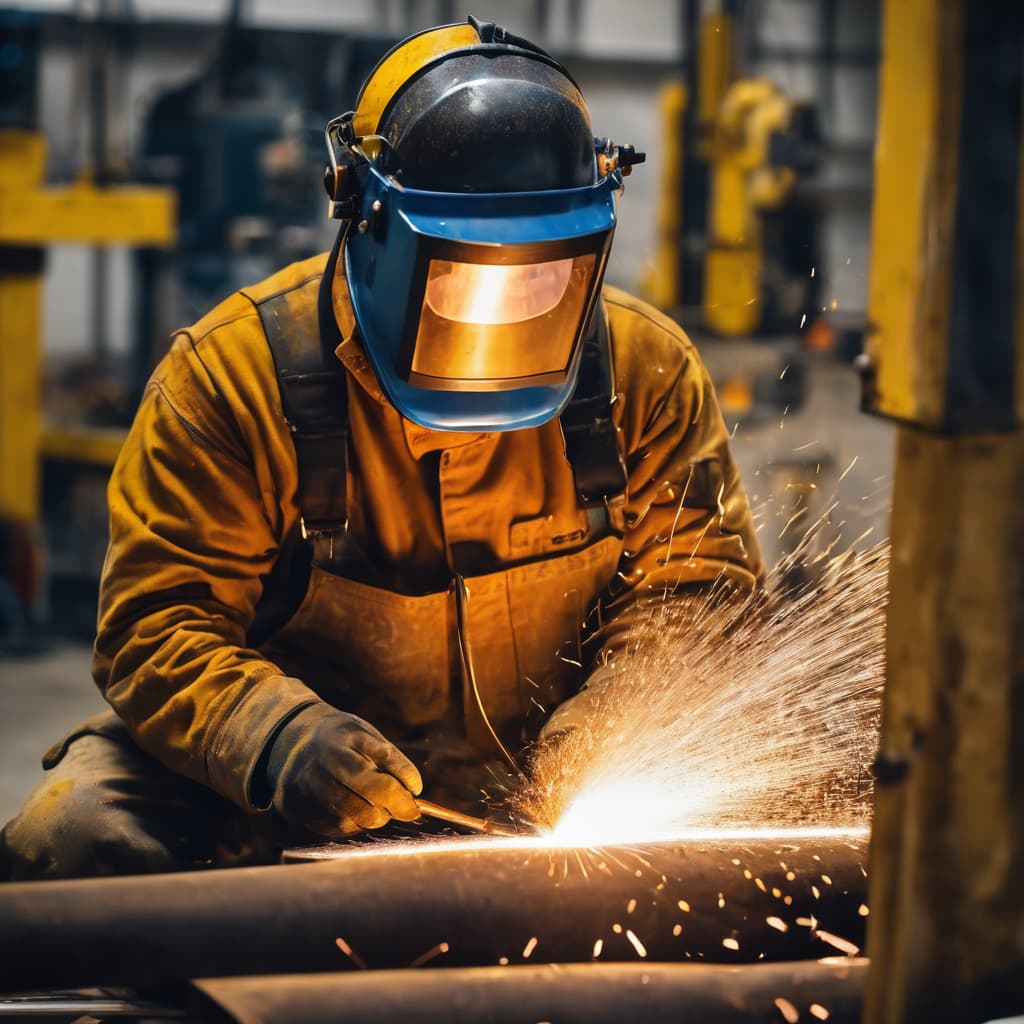
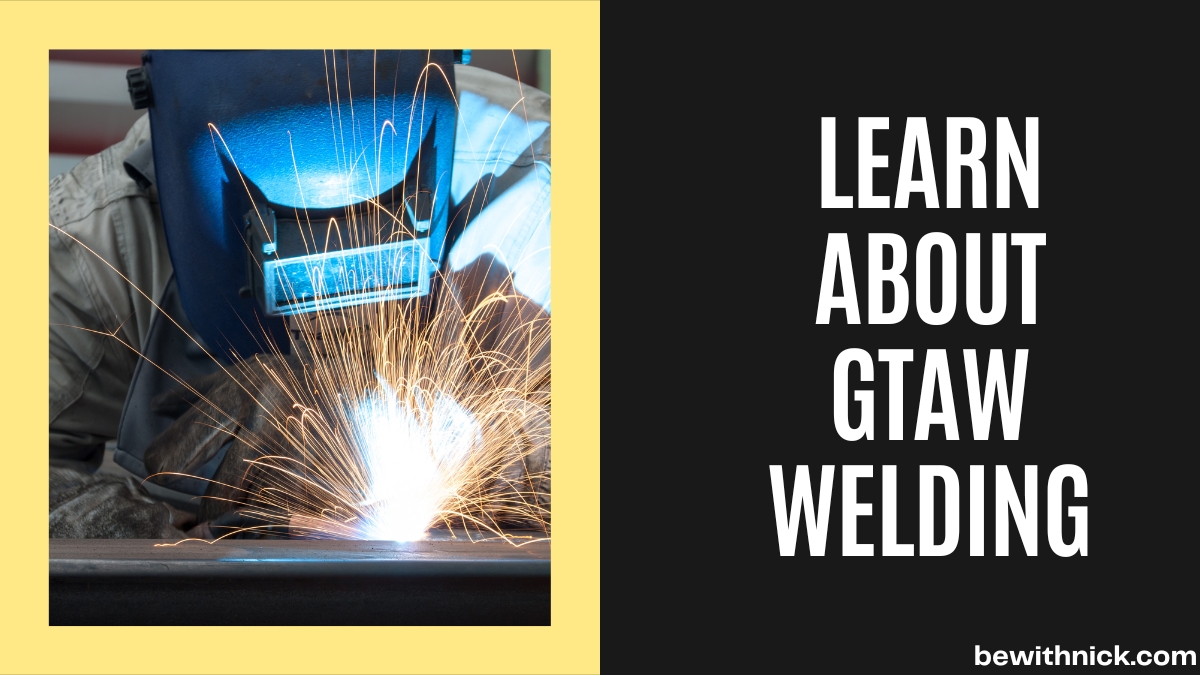